Occupational Safety
Rules create clarity
In the area of occupational safety we support you (consulting, risk analysis, control, action planning) in the fulfilment of your responsibility regarding safety at work, accident prevention, health protection and legal compliance.
In the case of accidents and occupational diseases, we offer you advice and support in the workplace and incident clarifications and in the determination of effective measures.
Asbestos
When handling potentially asbestos-containing material, the requirements of SUVA must be strictly adhered to. If there is a suspicion of asbestos, inform the safety officer.
Electrical Safety
Electricity - a «safe thing»? Yes, but only if in the hustle and bustle of everyday life the safety rules are not "forgotten".
- Electrical installations must be carried out only by professional electricians.
- Only use safety-compliant and well-maintained equipment. Check devices, cables and plugs regularly for possible damage.
- Study the operating instructions and follow the safety instructions contained therein. The instructions often also contain information about the maintenance intervals.
- Operate electrical appliances using a residual current device and only in rooms with a fire alarm system.
Explosion and Fire Protection
The objectives of the fire and explosion protection consist in the protection of persons, environment, property.
When working with flammable substances such as flammable liquids, gases or dusts, an explosive atmosphere may form.
The following safety measures have to be taken:
- The formation of an explosive atmosphere must be prevented or at least restricted (EX-zones), e.g. with ventilation measures.
- There must be no sources of ignition in explosive areas.
- For certain conditions, e.g. great damage potential, additional constructive explosion protection measures must be taken.
Explosion protection - Principles, minimum regulations, zones (SUVA leaflet 2153)
Checklist: Explosion risks (SUVA 67132 D)
External Employees
External employees working in the DBMR (e.g. insel-staff, TKI, Pathology) must comply with the DBMR safety regulations to ensure occupational safety and health protection.
Checklist: Cooperation with external employees (SUVA 66092.D)
Personal Protective Equipment (PPE)
Personal protective equipment (PPE) is an important element in ensuring the protection of workers and their physical integrity. The decision on whether and which personal protective equipment (PPE) is required is made after the assessment of the working conditions in the context of the risk assessment.
In principle, there is personal protective equipment for almost all hazards that can occur during work.
Respiratory Protection
To protect against particles / fine dusts, a disposable fine dust mask is sufficient. There are different filter classes:
- P1: up to 4 times the MAK-value
- P2: up to 4 times the MAK-value
- P3: up to 4 times the MAK-value
Masks against gases, vapours and particles have different filters for different hazards. Full masks or half masks are used. Full masks cover the face and therefore also protect the eyes. Half masks enclose mouth, nose and chin. Depending on the application, an additional eye protection is necessary.
The following questions help you to choose the right respiratory protection:
- Which hazardous substances are present?
- Do the masks serve as protection against particles/fine dusts or should they protect against gases and vapours?
- In which state of aggregation is the substance?
- Can I smell or taste the hazardous substance?
- What are the normal workplace concentrations?
- How many hours/per day the employee(s) need(s) to wear it?
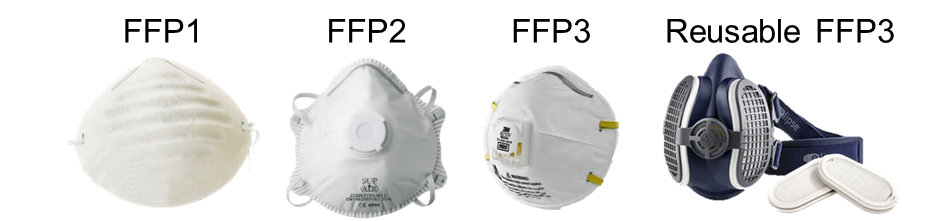
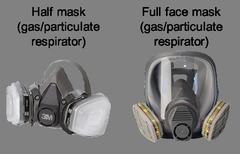
Eye Protection
Eye Protection
Safety specs protect from chemical, mechanical, thermal, biological, electrical, radiological or simply weather associated hazards. Also face shields may serve as an eye protection, but sometimes it has to be combined with safety goggles according to the risks. WEARING SAFETY SPECS IS MANDATORY IN ALL DBMR LABORATORIES. Laboratory safety specs are provided by the DBMR supply center free of charge.
Ear Protection
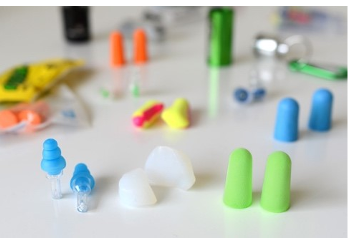
Ear Protection
A decreasing hearing performance is usually noticed late and is irreversible. If noise >80 db can’t be eliminated by technical or organizational measures, ear protectors needed. If noise can not be avoided through technical or organizational measures, then you need the right ear protection. The choice depends on the personal wearing comfort and the purpose.
Skin and Hand Protection
Gloves protect against thermal, mechanical, chemical hazards, microorganisms or ionizing radiation.
Prior to procurement, it must be determined on the basis of the risk assessment which glove can be used. Choosing the right glove is a difficult decision.
Protect your skin! We help you to create a skin protection plan:
- Skin protection creams are used before starting work. They protect the skin against the various influences in an aqueous or non-aqueous environment and facilitate the cleansing of the skin. Use skin protection cream before starting work.
- Skin care: Skin care cream should also be used several times a day (after washing hands before breaks, after hand disinfection and at the end of work).
Protective Clothing
Which protective clothing you need is determined by the risk assessment.
Wearing a lab coat or lab apron is mandatory in all DBMR laboratories. Protective clothing must not be washed at home, but only by the hospital laundry.
Application form for the free loan of work clothes in exceptional cases
Safe Apprenticeship and Protection of Adolescent Employees
Safe Apprenticeship
The employer specifically introduces learners and provides occupational safety systematically and comprehensibly from day one. Trainers, supervisors and employees support them.
Protection of Adolescent Employees
Contact person: François Achermann
Adolescent employees (≥15yo) are covered by the Youth Employment Protection Act and are not allowed to carry out a dangerous work, except in the context of vocational training and if it is indispensable for the learning process and the accompanying occupational safety measures specified in Annex 2 of the Vocational Education Regulations are complied with.
Risk Assessment
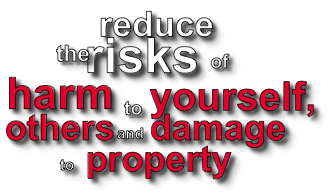
Identify and reduce risks
Risks can only be dealt with if they are known. The risk assessment leads step by step to the optimization of working conditions.
The DBMR uses the webtool "SAFELY SWISS" provided by the University of Bern for the risk assessment with checklists to systematically identify hazards.
SAFELY SWISS is also used plan and administrate safety measures. Suitable measures must be taken to eliminate the dangers identified or reduce them to an acceptable level. It must be ensured that the measures taken remain effective in the long term.
Process step | DBMR safety | Responsibles in the organizational unit | Safely Swiss web tool |
---|---|---|---|
1) Announce risk assessment | Plan, Do | Check | |
2) First meeting and inspection of the work areas | Do | Do | |
3) Prepare checklist | Do | Act | Yes |
4) Fill in checklist | Act | Do | Yes |
5) Discussion of the results and safety measures needed | Do | Do | (Yes) |
6) Plan safety measures | Do | Act | Yes |
7) Accept or reject planned safety measures | Check | Do | Yes |
8) Notify fulfilled safety measures | Check | Do | Yes |
9) Announce reeassessment after 3 years or as needed | Plan, Do | Check |
Work Equipment
Defects in work equipment that are not detected and eliminated before the first start-up can be the cause of accidents, damage to health and much more. Following such events, criminal or civil penalties for manufacturers, distributors and employers are not excluded.
Through the CE mark a manufacturer in the European Union declares that a particular product meets the applicable requirements set out in the relevant harmonization legislation and this has been demonstrated with the corresponding conformity assessment procedures. The CE mark ensures that the labelled products can be traded without restriction in the EU and guarantees the consumer within this area uniform protection in health, safety and environmental matters.
Work equipment must be maintained according to manufacturer's instructions.
The maintenance must be carried out by suitably instructed or trained persons.
The executed maintenance must be documented. This can be done in a simple way: Who has maintained what and when.
Checklist for work equipment (SUVA 66084/2.D) (Checklist for work equipment)
EKAS Guideline Work Equipment Nr. 6512 (Guideline for work equipment)
Working Alone
Working alone is not permitted if the work can lead to injury, that requires the immediate help of a second person.